Feeder for assembly line.Central component supply with 3 drop-off points.
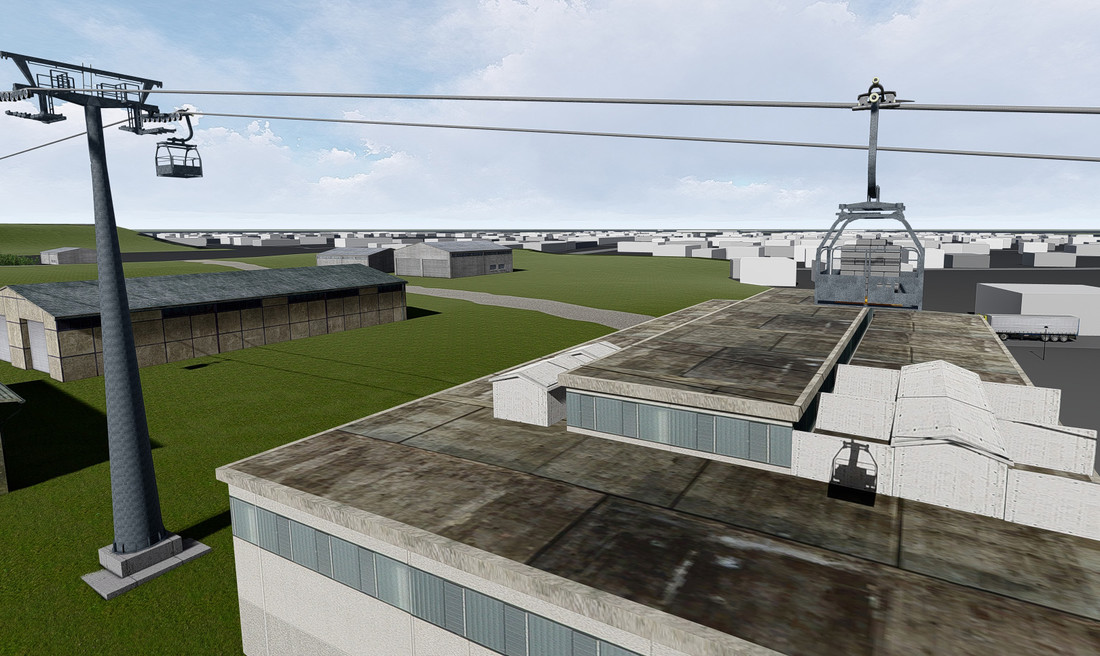
Customer requirements:
Three assembly halls of an automobile manufacturer must be continually supplied with new car components. The sub-supplier's warehouse, however, is several kilometres away. There is densely built-up infrastructure between the loading station and the destination points. 60 units of two pallets each per hour must be transported to each assembly hall and the empty pallets retrieved and taken back. One pallet weighs approx. 500kg, and one transport unit therefore approx. 1 ton. In order not to delay the assembly process a very high availability must be guaranteed.
Our solution:
The densely built-up industrial area and therefore the need to save space suggest using a ropeway with detachable carriers. Two pallets each are loaded into one carrier which is attached to a continually moving haul rope. In order to supply the components to the three different destinations, two independent ropeway systems will be used: Ropeway 1 will supply components to hall 1 and take back the empty load carriers. With halls 2 and 3 in a straight line, only one ropeway system will be required for this process. For hall 2, which is located before hall 3, an intermediate station will be provided where the carriers intended for this hall will be separated from the haul rope and unloaded. After the returns have been loaded onto the carrier, it is attached to the haul rope again and travels back. The carriers for hall 3 will pass through the intermediate station without stopping.
System: | Ropeway |
Transported material: | Pallets |
Horizontal length: | 3,200 x 2,600 m |
Vertical rise: | 0 m |
Conveying capacity: | 60 pcs/h |
Payload per carrier: | 2 x 500 kg |
Motor rating, continuous: | 330 kW |